Colorado economists warn of rising home prices, job losses as tariffs hit construction materials
Colorado experts say tariffs on building materials will hurt small businesses and worsen the housing market. A builder in Colorado thinks it’s a necessary evil.
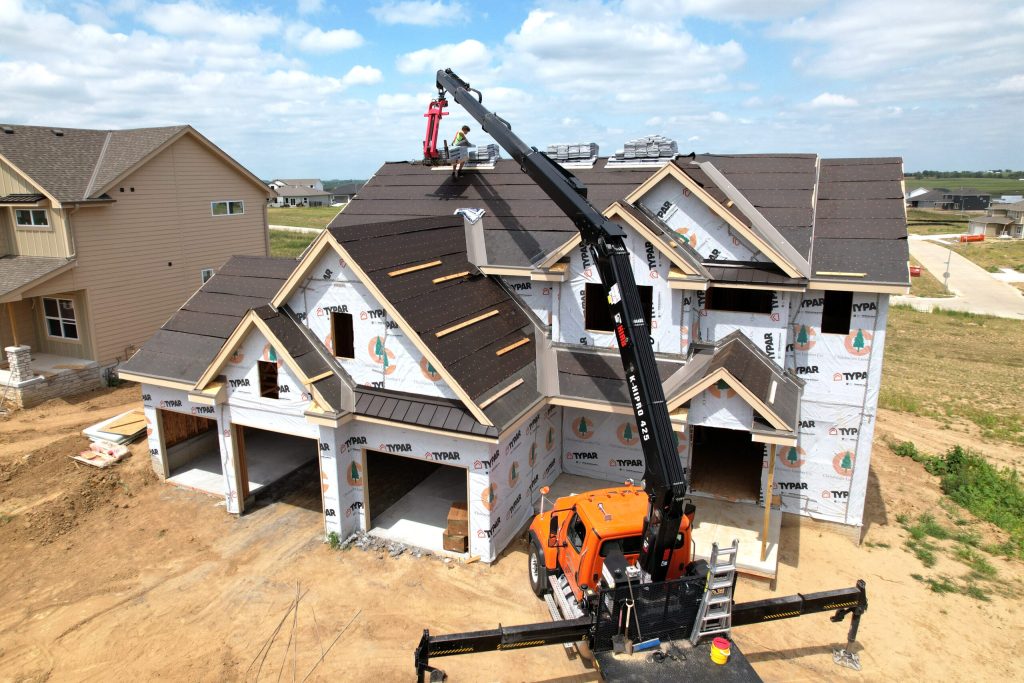
Courtesy/Kodiak Building Partners
Builders in Colorado are bracing for tariffs on common construction materials like steel and aluminum to move down the chain. Some experts predict the end result will likely bring up home prices and lose business for local contractors that can’t absorb the cost increases, but others argue it could be good for business in the long run.
In March, President Donald Trump reinstated 25% tariffs on steel and aluminum imports. The move was pitched as a way to strengthen domestic production of both materials, though some Colorado economists argue it could raise the cost of construction in a state where high home prices are already a barrier to housing.
“We’re concerned with any policy that disrupts predictability in the market or increases the cost of doing business, whether that comes from the state or federal government,” Colorado Chamber of Commerce President and CEO Loren Furman said in a statement. “Specifically for Colorado, which is already one of the most expensive states to live and do business, tariffs could seriously interfere with our work to improve competitiveness and the broader economy.”
Tariffs on both products were first imposed in 2018 during Trump’s first presidential term — 25% on steel and 10% on aluminum — before they were sequentially adjusted by the Biden administration. Because steel and aluminum are essential materials in residential and commercial construction — used in everything from beams and HVAC systems to roofing and appliances — builders saw a significant rise in material costs.
Costs for construction materials rose almost 9% nationally from May 2017 to May 2018, driven largely by the steel and aluminum tariffs, according to data from the Associated General Contractors of America. As the costs were passed down the chain, many builders either delayed projects or increased home prices to maintain profit margins.
Trump’s reinstated 2025 steel and aluminum tariffs are broader, with fewer exemptions on specific products and countries than before. As opposed to 2018, the scope of the tariffs has been expanded to cover not only raw steel and aluminum but also a range of products made from these metals, such as nails and wires.
Paired with tariffs on other construction materials, including lumber, the National Association of Home Builders estimates it will soon cost roughly $9,200 more to build a single-family home — not counting impacts from the flurry of reciprocal tariffs announced on April 2.
“The president will claim until he’s blue in the face that foreigners pay the cost of these tariffs. It’s simply not true. Tariffs are passed through in the higher costs at the input stages and all the way through the consumer goods stage,” CU Boulder Professor of Economics Emeritus Keith Maskus said. “People in Colorado will experience an increase in the cost of living, there’s no question about it. And it will happen sooner than they might think.”
Higher material prices for businesses — and eventually, consumers
Tariffs are taxes placed on imported goods, making them more expensive to companies in the U.S. wanting to buy foreign materials or products.
Nationally, roughly a quarter of all steel and half of all aluminum used in the U.S. is imported, according to data from Reuters. Despite having an active forestry industry, the country also remains a net importer of lumber, making it unlikely that any industry will manage to avoid the tariffs’ impacts.
Steel and aluminum are commonly used in the manufacturing of automobiles, appliances and electronics and are found in building materials like structural frames and roofing. When paired with lumber — which currently has a 10% tariff — both builders and consumers are anticipating higher housing prices in Colorado’s already inflated housing market.
“I’m sure there’s a lot of construction going on around the Western Slope, so I suspect that the biggest negative impact will be there — it means increased prices and probably fewer contracts because of the cost of production,” Maskus said.
The Trump administration is marketing the tariffs as a way to promote domestic buying while deterring foreign steel and aluminum imports. However, the increased demand for domestic suppliers as builders flee from the heightened prices of foreign imports traditionally results in domestic suppliers raising their own prices — which rarely come back down after tariffs are lowered.
“These domestic steel producers are now in a position to say, ‘You know what? We can raise our prices because there’s a lot more demand for our products,'” Maskus said.
“If these tariffs remain in place for a few years, I think over a matter of 12 months, you’ll see the cost of these imported steel and aluminum inputs go up by 20% to 25%, and then that would mean spillover price impact on domestically produced inputs of about the same magnitude,” he added.
Though the tariffs may drive some construction companies to switch from foreign to U.S.-based suppliers, which is good for keeping local money in Colorado’s economy, that switch can take time — especially when many companies have contracts in place with foreign suppliers.
Small businesses will suffer the most, economist warns
Larger construction companies have an easier time managing the higher prices and increased demand that traditionally accompany tariffs. They’re able to absorb more costs without significantly raising their prices, at least in the beginning, and secure better prices on construction materials by buying in bulk, Maskus said.
Small businesses and contractors in Colorado, especially those in the residential construction and renovation sectors, work within thinner margins and are forced to pass more material costs to their bids.
“I think you’ll see a lot of these (smaller) contractors losing business fairly quickly, whereas the big construction companies … have more scope to absorb some of those cost increases into their own pricing and not raise their prices as much, even if they can’t do it forever,” he said.
Because of the reliance of other sectors on steel and aluminum for machinery, everything from solar panel installation to agriculture work will face higher prices on necessary equipment.
“In the case of Colorado, I think farmers will see a big hit there,” Maskus said. “If I were a farmer and I needed a combine or a tractor or something soon, I think I’d be buying it right now, if not last year.”
Could Colorado see more domestic jobs from the tariffs?
As of February 2025, there were roughly 180,000 construction workers in Colorado, according to U.S. data from the Federal Reserve Bank of St. Louis.
Because tariffs give domestic producers a price advantage and incentive to expand their employment, Trump’s 2018 tariffs did create more jobs in the steel and aluminum sectors nationwide, though the gains fell short of the administration’s expectations. Maskus said this is because a lot of the money gained domestically went into automated processes and machinery more than employment. On the other hand, other sectors lost jobs because of the increased steel costs.
“The costs that were imposed on other sectors who had to pay for this higher-cost deal were pretty significant,” Maskus said. “The sort of point estimates we have suggests that something like 4,500 or 5,000 jobs were destroyed inside the metal-using sectors, especially in construction, because steel is so important as an input there.”
This time around, he is predicting a similar outcome.
“My best expectation is that you’re not likely to see much positive supply response in the steel and aluminum sectors in Colorado but a fairly substantial penalty imposed on these various other sectors, especially including instruction,” he said.
Are tariffs a necessary evil to fix the housing market? Another point of view
Steve Swinney, chief executive officer of Colorado-based construction supply company Kodiak Building Partners, said the volatility of the tariffs has created some short-term uncertainty for his company — though he expects it will pay off in the end.
“It creates a lot of questions. You spend a lot of time thinking about, ‘Well, how much inventory should we have right now? How much should we be buying in this? How should we be pricing it?'” Swinney said. “All that uncertainty is bad for business in the short run; it just creates a lot of extra concern, worry throughout the supply chain, with our customers as well. How do I price the home to the consumer when I don’t know how much the lumber or the steel that goes into it is going to cost next month?”
The largest use of Kodiak’s building materials is for building single-family homes, which Swinney said have become incredibly unaffordable in Colorado. Though he expects the worst of the tariffs to bring home prices up by 2.5% in the long run, he said higher housing prices brought on by interest rates and regulatory costs are what have driven Colorado’s long-standing affordability issue.
“Of course, (the 2.5% increase) is bad,” he said. “But at the end of the day, it’s not fundamentally changing the game. We already had a big affordability issue.”
Despite the initial pricing hurdles, Swinney described the tariffs as “really necessary” for long-term stability in the housing market — which he said is a different perspective on the tariffs than what he’s heard from others in the industry.
“Without addressing longer term interest rates in particular, we won’t get to where we make homes more affordable for people,” he said, adding that driving down interest rates would mean lower mortgage rates for homeowners. “The short-term is really uncertain, (but) I think (the tariffs) are ingredients of what we’ve got to do to get longer-term rates down.”
In the time that it takes for tariffs to either stick or go away, he said his team has a few strategies to avoid taking too many financial risks as the impacts of the tariffs settle in — especially when it comes to deciding whether to buy more inventory or “wait and see.”
“It’s definitely impacting both our suppliers, our customers and us in terms of how we manage through this uncertainty,” he said. “All of it is forcing everyone to really reevaluate their playbook.”
For now, Swinney’s team has opted to carry as little inventory as possible, so that Kodiak Building Partners can quickly reset its cost structure as things shake out and communicate the changes with its partners. He said it’s possible that other builders and home buyers might respond by building smaller homes to offset the additional costs.
“If we carry a lot of it to begin with, then we’re fundamentally making a bet that prices are going to go up,” he said. “We just don’t know right now.”

Support Local Journalism

Support Local Journalism
Readers around Craig and Moffat County make the Craig Press’ work possible. Your financial contribution supports our efforts to deliver quality, locally relevant journalism.
Now more than ever, your support is critical to help us keep our community informed about the evolving coronavirus pandemic and the impact it is having locally. Every contribution, however large or small, will make a difference.
Each donation will be used exclusively for the development and creation of increased news coverage.